Don’tpitcustomerserviceagainstdailyefficiency.
It’sanexpensive
illusion
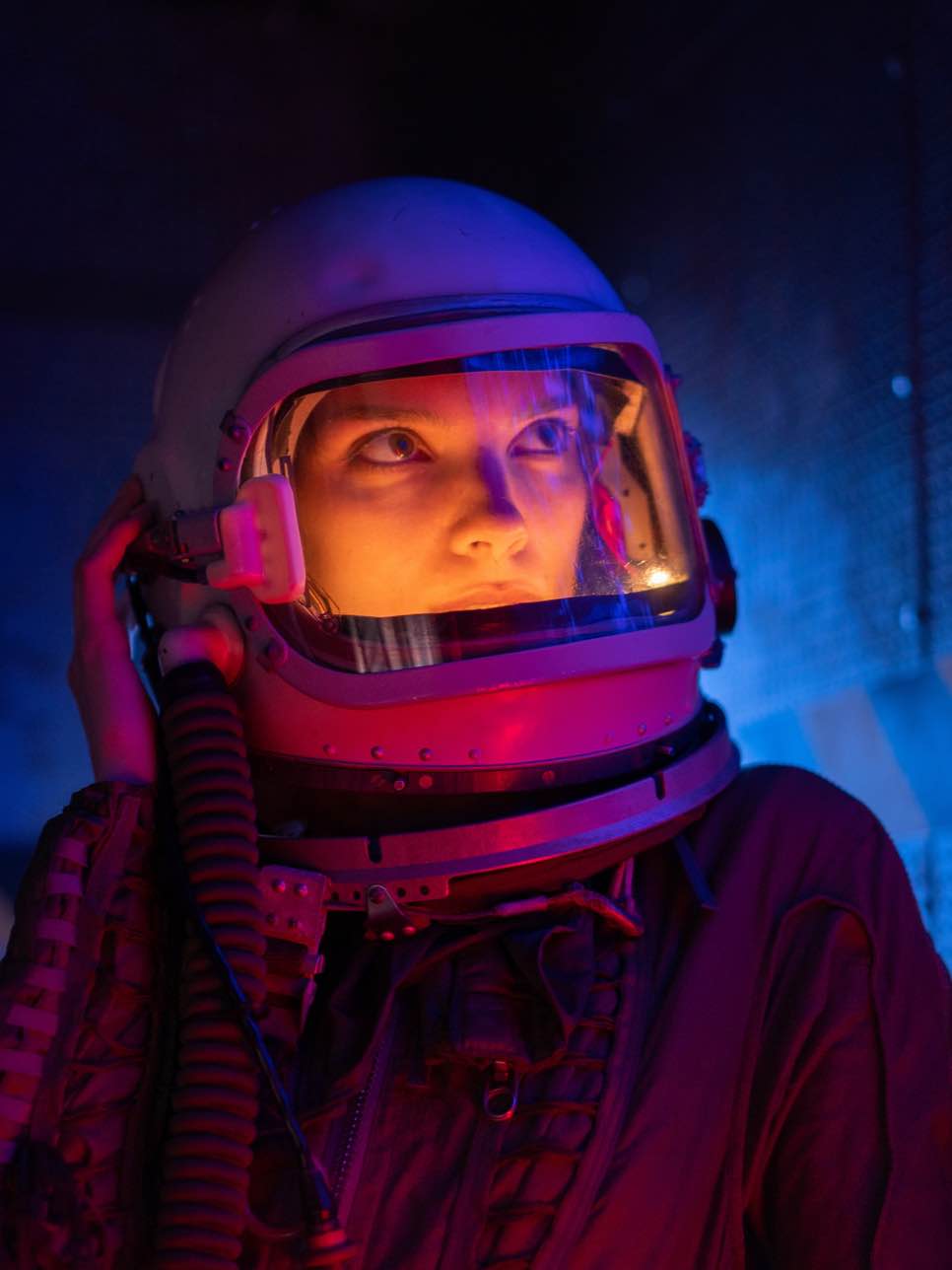
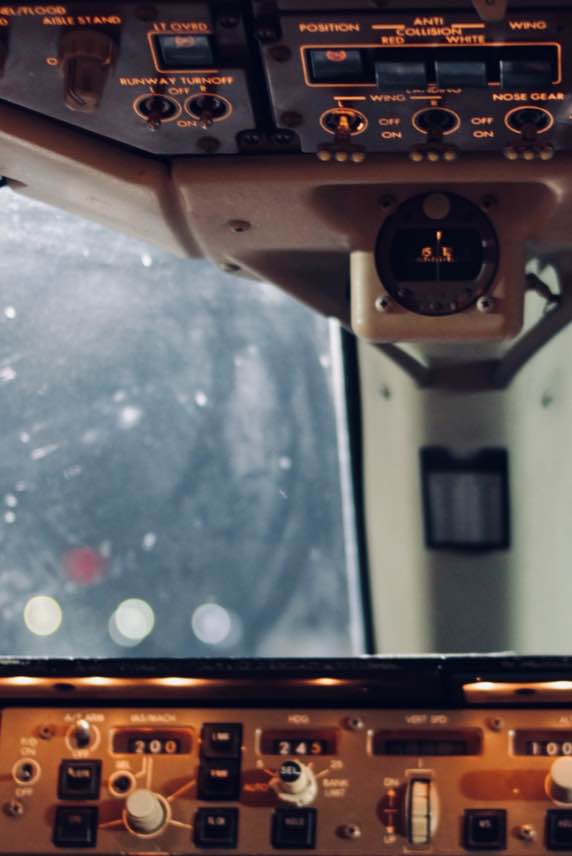
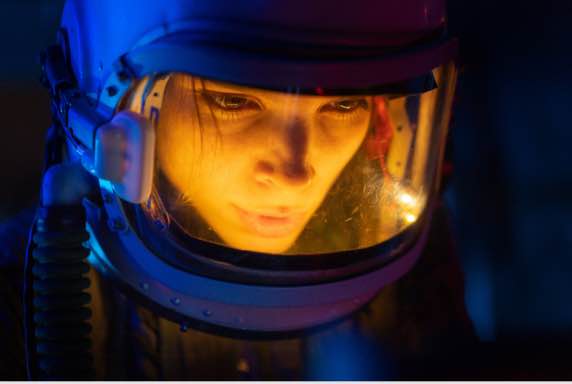
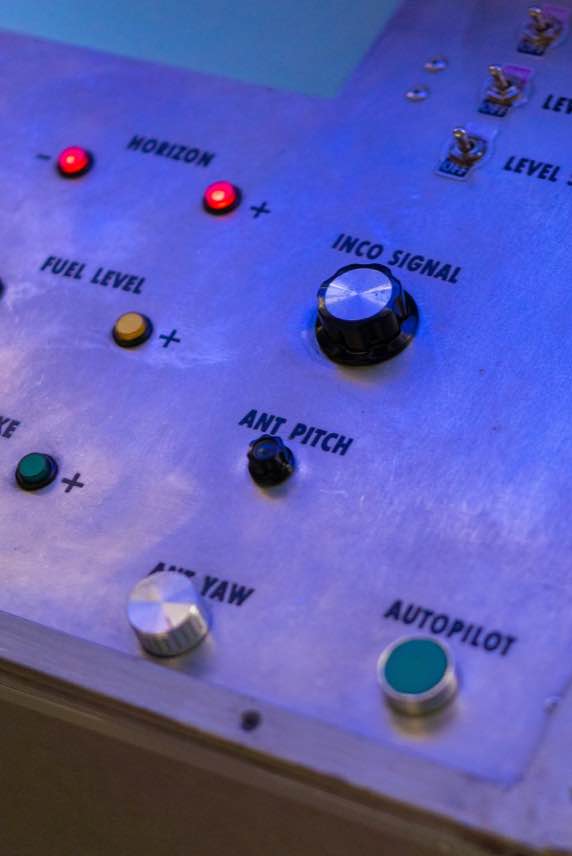
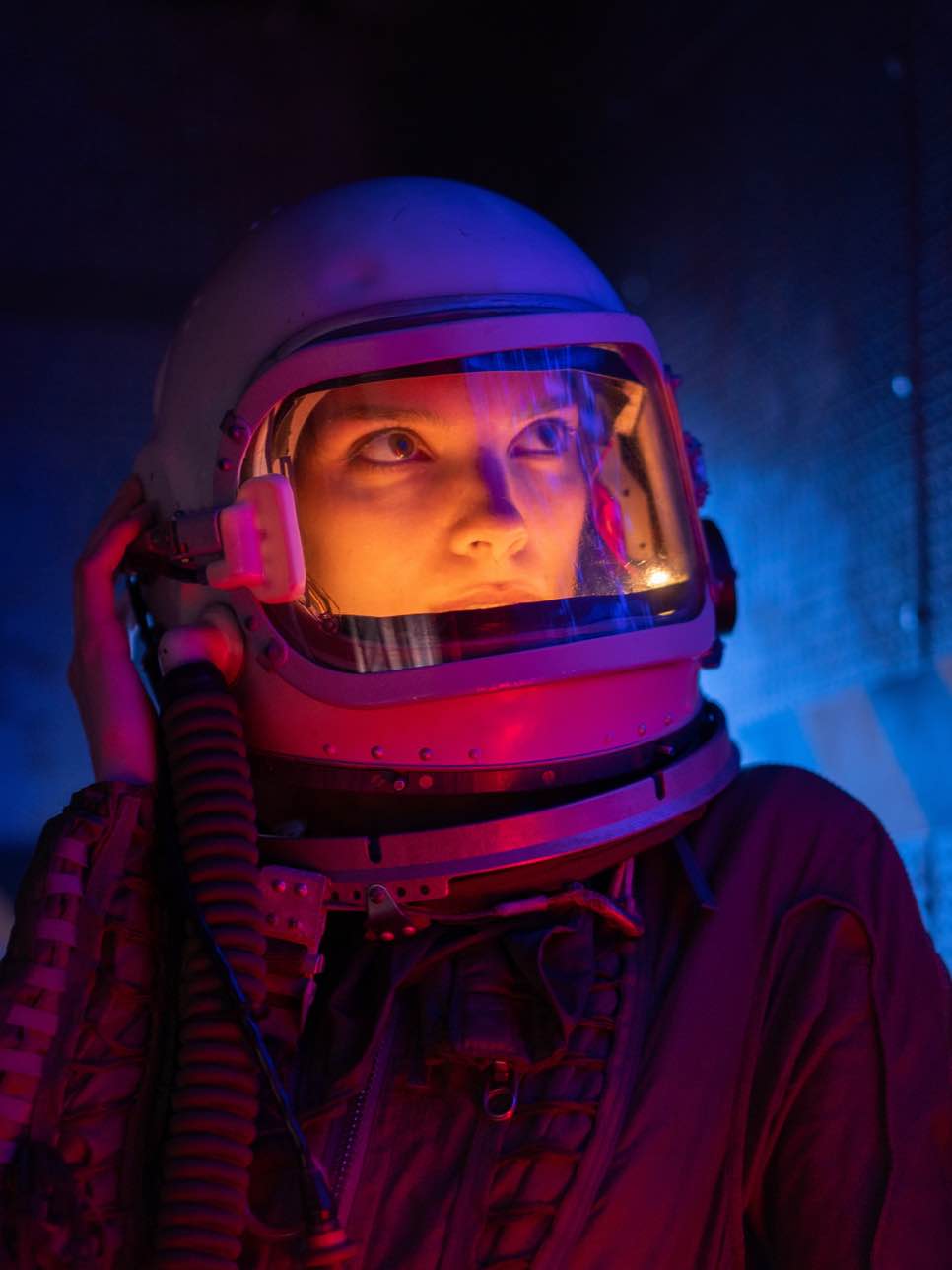
In an era where performance is no longer an option, inefficient daily activities lead to dissatisfied customers. Your profits dwindle,
and your productivity is reduced by ineffective processes.
70% of customers are less likely to do business with a company that has operational inefficiency issues (Forbes Insight).
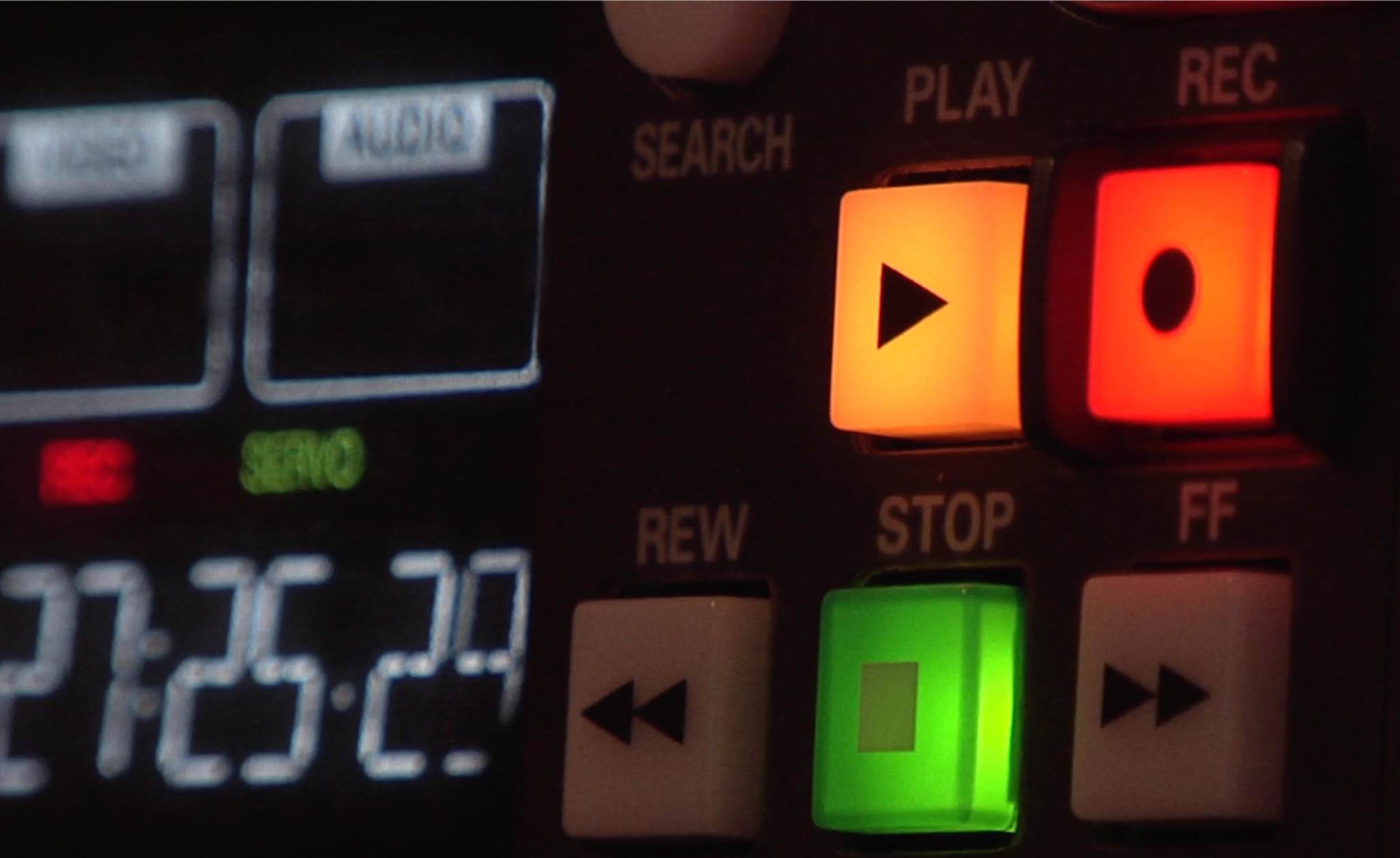
Why?
Because the root causes of waste and customer dissatisfaction are the same:
long delivery times, order errors, etc.
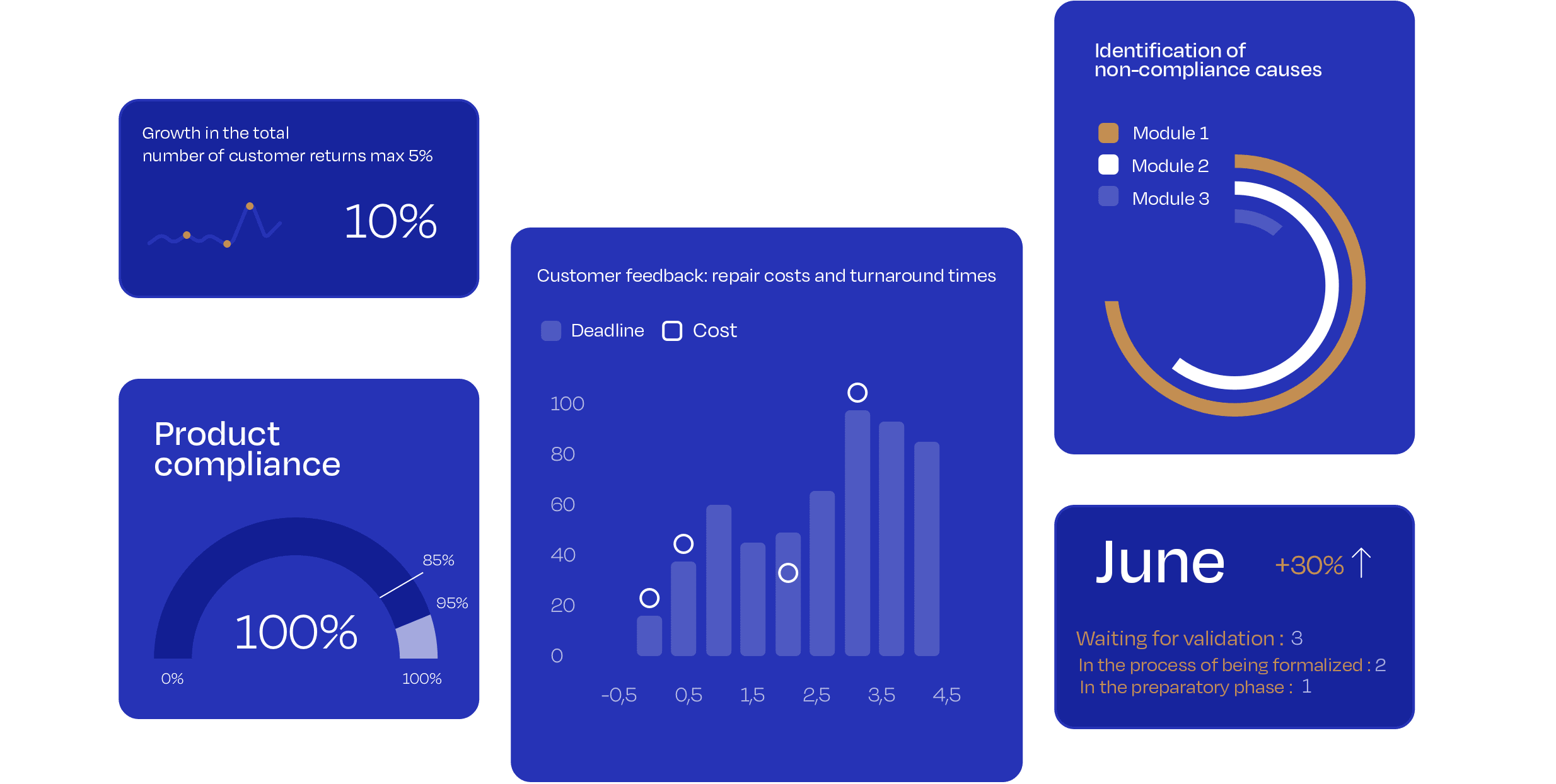
Instead, understand
what your customers value most,
and rally your teams around it.
Productivity will increase.
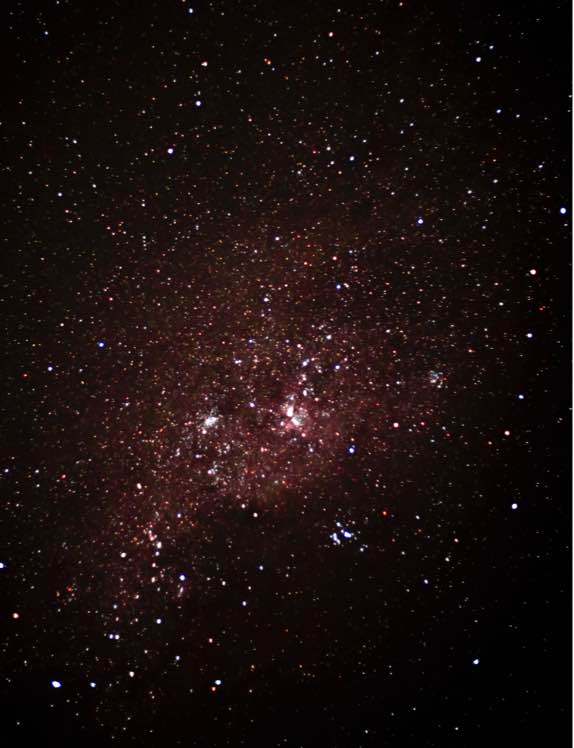

Aim for excellence
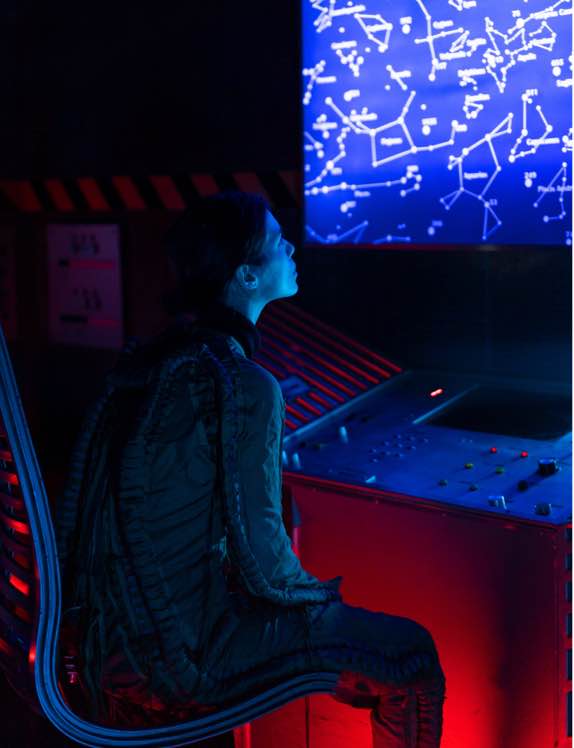
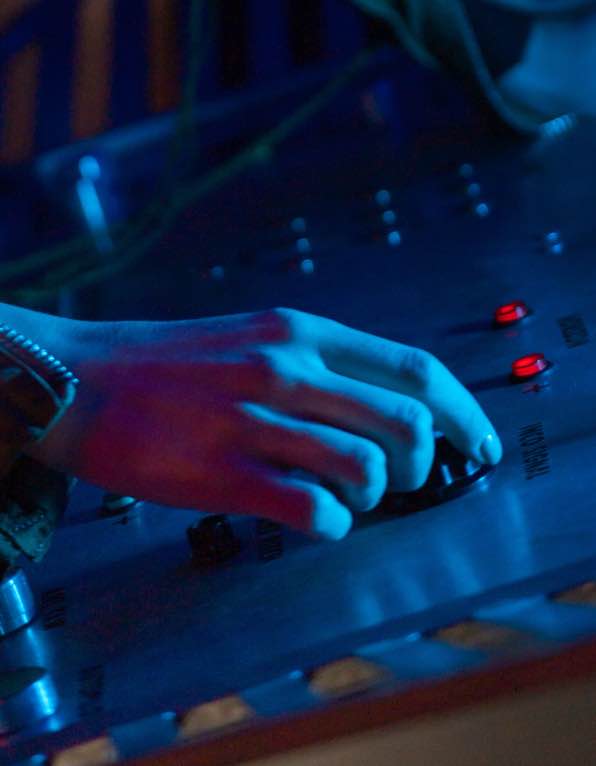
Maximise results
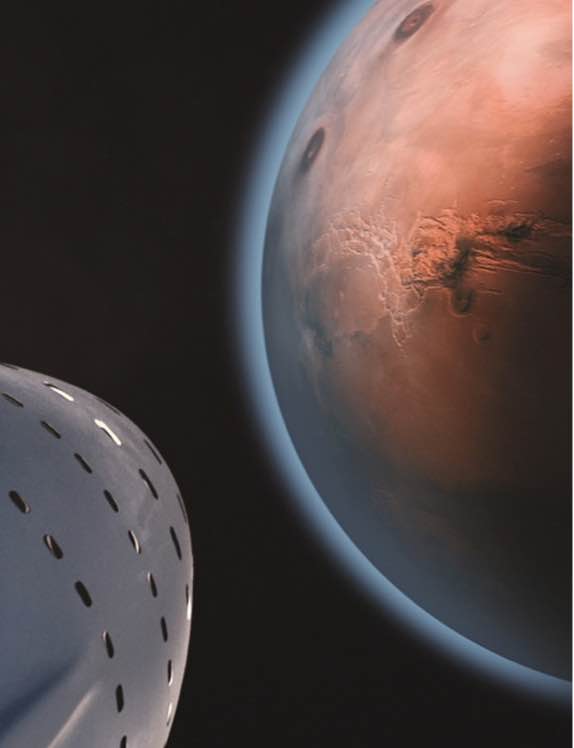
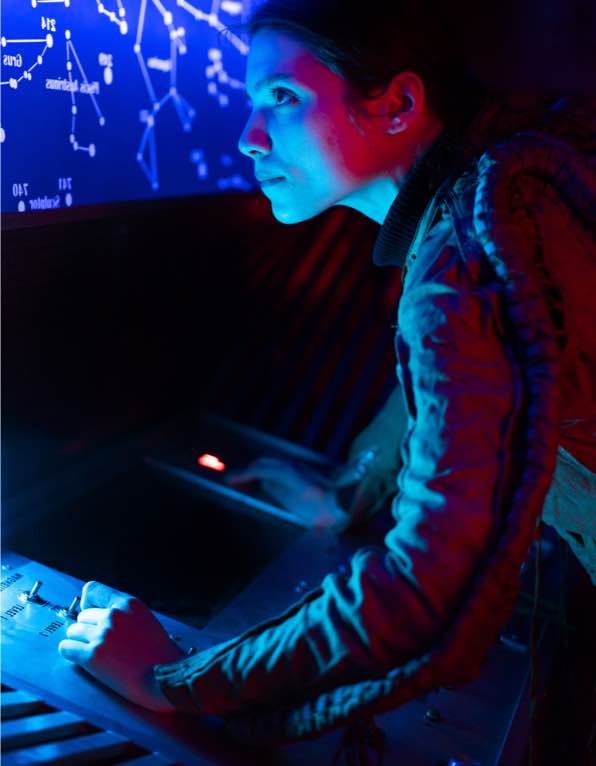
Perform as a team
Our added
value
Optimised performance
01.
Constant improvement
02.
A united and high-performing team
03.
Operational excellence
By Ad Valoris
Comprehensive guide to operational excellence
IF YOU HAVEN’T DONE IT ALREADY, AIM FOR OPERATIONAL EXCELLENCE
An organisation without an operational excellence approach risks wasting its efforts.
By focusing solely on cost reduction, you risk neglecting crucial dimensions such as customer experience, a culture of continuous improvement, and human impact.
With an integrated approach to operational excellence, you optimise not only your resources but also opportunities, while making more effective decisions.
Integrated operational excellence gives you a competitive edge, aligns your teams with common goals, and provides the flexibility needed to adapt to changes.
Aim for operational excellence
and make your organisation
a model of sustainable performance
Let's talk clearly!
5 reasons to choose Operational Excellence by Ad Valoris:
You benefit from a structured approach focused on efficiency and quality.
You implement a continuous improvement system to stay competitive.
Your teams are motivated and engaged, thereby improving productivity.
You transform best practices into tangible and measurable results.
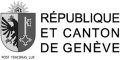
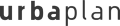
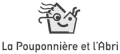
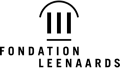
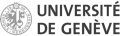
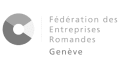
Our solutions for this service
To learn more
Are OKRs a simple method for performance management in business?
OKRs promote alignment, transparency, and organisational adaptability. ...
The usefulness of the management cockpit in decision-making
The management cockpit facilitates strategic decision-making within a company. ...
Managing an organisation through processes
Knowing how to anticipate challenges and seize the opportunities that arise. ...